28 fume cupboards upgraded in the School of Chemistry
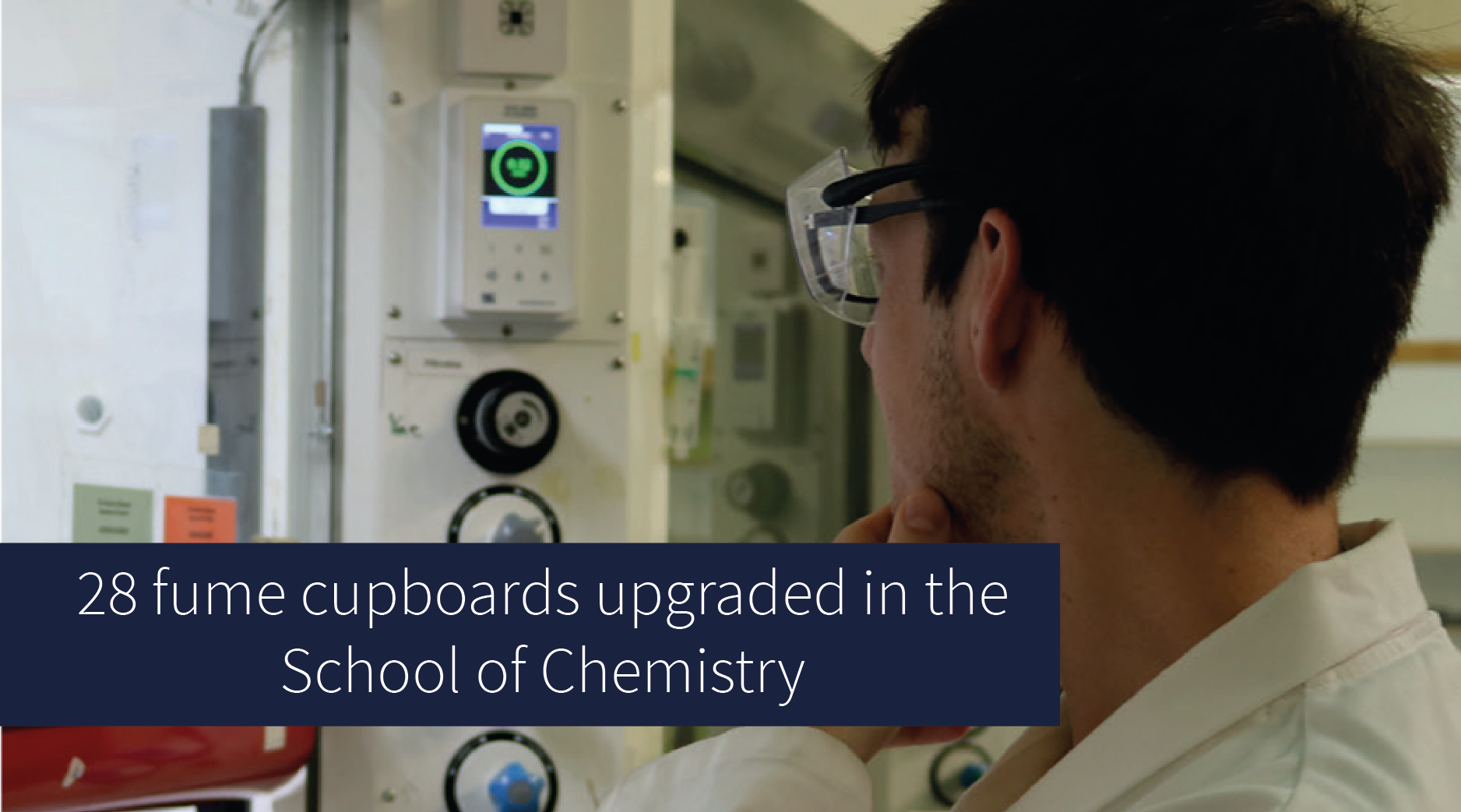
This Sustainable Campus Fund project will reduce heat and electricity consumption of fume cupboards by over 50%. Funding also came from the Scottish Funding Council.
This blog post was first published in 2020 as a Sustainable Campus Fund case study on the Department for Social Responsibility and Sustainability website.
Improving fume cupboard efficiency
The School of Chemistry was aware that many of its current fume cupboards were of the Constant Air Volume type. As the name suggests this type of fume cupboard expels a fixed volume of air when they are on – regardless of whether the sash is up or down. They applied for funding to convert these fume cupboards to Variable Air Volume systems, which can reduce the air flow when the sash is down. This maintains safety while also significantly reducing the amount of heated or cooled air extracted from the building, reducing the load on the heating and cooling systems of the building.
The Department for Social Responsibility and Sustainability, in collaboration with the School of Chemistry, identified and developed this project. The Estates Department’s Energy Team/Small Projects and Minor Works Team led on the project delivery.
Project details
Number of fume cupboards | 28 |
---|---|
Total funding awarded by the Sustainable Campus Fund and Scottish Funding Council | £275,000 |
Tonnes CO2 saved per year | 130 |
£ saved per year | £33,000 |
The technical bit
Ventilation plant: Variable air volume (VAV) boxes were fitted to allow control of the supply volume to adjoining rooms. A bleed air duct and damper were fitted to the extract duct to allow balancing of the extract air as the fume cupboard demand drops. This allows the escape velocity at the extract stack to be maintained.
- Fume Cupboards: Auto-sash closing mechanisms fitted with PIR motion sensor user presence detection and control interface. Volume control damper fitted to each fume cupboard extract duct to control the volume of air extracted from each cupboard in relation to the sash position.
- Controls: The system is controlled by the Building Management System (BMS). Additional room pressure sensors were fitted so supply air can be balanced. New control graphics were developed to allow monitoring of the system. This will allow the project performance to be monitored and any learning to be built into future projects.
- Fume Cupboard Lighting: The lighting in the fume cupboards was updated to LED during the project, providing additional energy savings and better lighting within the cupboards.
The result
Testing ensured the fume cupboards function correctly and confirms the optimal face velocity. Auto-sash closures ensure the sashes return to the closed position when not in use, which offers a better user experience and is safer too.
Estates Department
This case study was reformatted from the original case study compiled by the Estates Department.
What is the Sustainable Campus Fund?
The Sustainable Campus Fund is an internal investment vehicle that finances projects within the University that will improve energy efficiency or use or produce renewable energy, as well as other types sustainability projects that generate cost and carbon savings. The fund is managed by the Department for Social Responsibility & Sustainability and delivered in partnership with the Estates Department.
Anyone at the University – staff and students – can propose projects for the fund. Once a project is proposed, we will advise and support the development of the project before submitting it to the Utilities Working Group for approval.
Can you think of a project that will help the University to save carbon and generate cost savings? Register your interest in the fund and get support to develop your idea today.
Recent comments