When we board a plane, we don’t give its engines a lot of thought. Most of us take them for granted, not realising the great deal of work that happens behind the scenes to get us where we’re heading, safely. Edinburgh alumnus and engineer, Juan Carlos Fallas-Chinchilla, shares how he got into the aerospace industry and what he does for one of the leading aero-engine manufacturers to keep us safe in the air.
Current treasured object: My turntable record player. This was a Christmas gift from my girlfriend as I started collecting vinyl records and did not have a quality one to listen to them on. Since then, it has been a great way to enjoy not only music, but I also really like the art on the vinyl covers. The turntable is a great talking point and fun to have on in the background when we have family and friends around.
Song of the moment: Black Hole Sun by Soundgarden. I love the 1990’s.
The first thing I noticed when I woke up this morning: My cats, ready to have breakfast!
———————————————————
Ever since I was a young child, I remember being curious about how things work; from toys, radios and buses, to planes and space shuttles. I used to read novels by Jules Verne, who wrote about fantastic machines and atmospheric travels long before aeroplanes were invented, and follow journeys of Franklin Chang-Díaz, a former NASA astronaut who, like me, comes from Costa Rica.
I attended high school near my hometown – Aserrí – where I trained in car mechanics. Thanks to the inspiring staff and my fellow students, I found real passion for hands-on and creative technical work. I then went on to study Mechanical Engineering at the University of Costa Rica.
When I was finishing my undergraduate studies, Ad Astra Rocket Company opened a laboratory in Costa Rica. They have a vacuum chamber to simulate space conditions and are building a space rocket called VASIMR that has the potential to take humans to Mars. The prospect of working on such an incredible project was very exciting. I decided to apply to do an internship and my final undergraduate project with them. To my delight, I was accepted.
Ad Astra Rocket Company is developing a propulsion system based on plasma, which is produced by heating gas until it is ionised and thrust is generated. I worked on the design of a heating system for plasma flow simulation, and helped the company test a ceramic tube that’s used to transport and heat the gas to ionise into the engine. The testing was done in high temperatures in a space-like vacuum environment.
My internship was a fantastic experience. Even though I no longer work there, I keep following the company’s progress on VASIMIR’s build. They have taken great strides through the years and the recent news about the improved engine performance are really encouraging and inspiring to see. What’s also interesting is that Ad Astra Rocket Company was founded by Franklin Chang-Díaz, the Costa Rican astronaut I grew up watching flying to space!
As an undergraduate student I met inspiring people who mentored me and encouraged me to consider different opportunities, including studying and working abroad.
My master’s degree then took me to the United States, where I studied Materials Science and Engineering at the University of Nevada. From there I moved on to doing research of materials at extreme conditions in places such as National Laboratories in the US and in Europe. After that, I realised I still wanted to pursue academic study, so I applied for a PhD at the University of Edinburgh.
My PhD project offered me the possibility of working in an area I had previous experience of, such as testing materials at extreme conditions (which is what I did in both Ad Astra Rocket Company and in the USA), while at the same time developing skills in computer stress analysis via FEA (Finite Element Analysis – a very relevant tool in engineering and industry).
For my PhD, I studied the stress performance of the Paris-Edinburgh press, an instrument developed jointly by the University of Paris and the University of Edinburgh. It is currently one of the most used high-pressure tools for neutron diffraction (a method to study the magnetic and/or atomic structure of materials at extreme conditions), available at many important research facilities around the world.
During my PhD, I also became a Chartered Engineer and volunteered in the Institution of Mechanical Engineers that offers fantastic ways for networking and staying up to date in engineering. I’m still a volunteer there.
As jet engine components are subject to extreme conditions, and their design and care involves stress simulations via FEA, my PhD from Edinburgh helped me to get my current job in aerospace, the sector I’ve been passionate about for as long as I can remember.
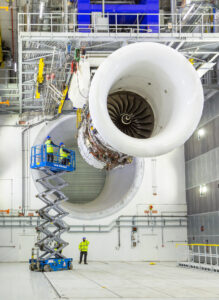
I now work in the Civil Aerospace division of Rolls-Royce, in the large aero-engines area. The engines we produce are designed and manufactured for long-haul aircrafts such as the Airbus A350 and A380, or Boeing 777 and 787. I started there in 2017 right after my viva exam and this is my first permanent job in the industry.
The story of Rolls-Royce is fascinating. The company began as a car manufacturer in 1906 and at the start of the First World War, in response to the nation’s needs, they designed their first aero-engine – the Eagle. The Eagle powered the first direct transatlantic flight as well as the first flight from England to Australia. Today, in Civil Aerospace only, Rolls-Royce has approximately 11,800 engines in service around the world and powers 35 types of commercial aircrafts.
During my first four years in Rolls-Royce, I worked in the Critical Parts and Safety area of the company, running complex computer models and primarily focusing on safety and airworthiness. I enjoyed the role, but as a trained Mechanical Engineer I have always had a fascination with the mechanics of materials. As I developed within the business, I looked for an opportunity with a focus on generating the data that was used in the models I had been running.
For decades, air travel has been tightly regulated to ensure safety of passengers. These tight regulations agreed by manufacturers and airworthiness authorities are in the public interest and aim to keep the safety bar as high as possible.
In January 2022 I moved to the Steels and Light Alloys team in the Materials Department, where I am currently based. My job in ensuring safety is by understanding the use and mechanical behaviour of materials throughout the life cycle of an aircraft engine including development, design, manufacture and in-service performance.
Among other tasks, we test a wide range of materials, including titanium and steel alloys, used in different parts of plane engines. My team explores the performance of these metals under operational variables such as cyclic loads (continuous and repeated stresses on a material), high temperature, and corrosive environments, among others. Our analyses are done in normal operational conditions as well as in remote scenarios of much higher loads and temperatures to achieve safe operation of parts. We then take well-informed technical decisions based on evidence, to support the company to establish a safe and reliable life span for the components and forecast when they need replacing.
The internal components of a jet engine are subject to high values of stress, temperature changes, and other variables during the flight. Corrosion, creep and fatigue also shorten the life span of the engine’s components. Understanding how different materials behave in these extremely complex scenarios is therefore incredibly important in order to accurately forecast their replacement and increase the safe life of the internal parts.
Aero-engines are amongst the most advanced engineering products in the world and the materials involved in their safe operation are complex. As a large team across different areas of the business we all deal with unique pieces of a giant puzzle.
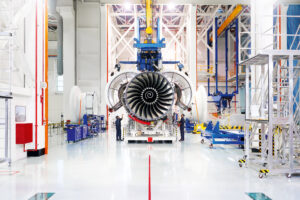
In my work, I also collaborate with university laboratories, other units of the business located overseas, and local stakeholders in the company. I really enjoy interacting with people from different departments and working with colleagues at various stages of their career. I have learned from colleagues with years of experience in the aerospace sector but also from new starters and apprentices on the shop floor. In Materials Engineering there is something new to be learned every day. I enjoy how the Materials Engineering community in the company trust and rely on each member to deliver in their area of business as most tasks require multiple teams to work together to produce a fruitful outcome. No matter if a colleague is based in Europe, America, or Asia, if you need a piece of information there is always someone willing to help. I also love how diverse and multicultural my workplace is.
When I was in technical high school studying to be a car mechanic, I never imagined my career would take me to so many countries. Now working in Rolls-Royce, I am motivated to continue working in the aerospace sector, which offers plenty of opportunities and stimulating challenges. Every day I get surprised by new information or a new task!
Links and sources:
© Banner photograph: Juan Carlos outside Rolls-Royce site in Derby; courtesy of Juan Carlos Fallas-Chinchilla.
© Other images courtesy of Rolls Royce; source Flickr.